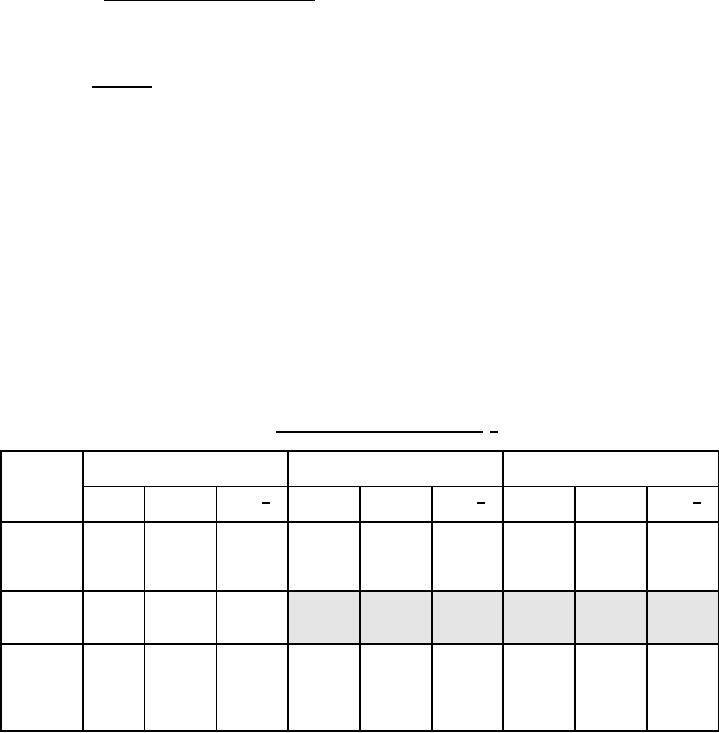
MIL-DTL-6162C
addition, Phase C operation may be terminated at a drive speed less than the specified value provided the total
horsepower - second output of the starter is equivalent to that which would be required to accelerate a frictionless
system to the specified cutoff speed.
If replacement of parts is required during the endurance test this shall be cause for rejection. Supplemental cooling
air may be used to expedite testing and prevent excessive temperatures. Total brush wear shall not exceed 50 percent
of the allowable wear on any one brush and commutator wear shall not exceed 25 percent of the total allowable
reduction of diameter. Allowable wear shall be as specified by the manufacturer and approved by the procuring
activity.
4.6.18.1.1 Starter endurance alternate method. If a drive stand equipped with an engine simulator is available,
both the consecutive start-cycle tests of paragraph 4.6.15 and the endurance test may be performed using this
equipment. The simulated moment of inertia and engine drag torque characteristic shall be adjusted to the maximum
starter design limits as specified on the associated specification sheet.
4.6.18.2 Generator.
a. Air-cooled generators shall be subjected to the endurance test schedule of Table II under the conditions
outlined in Table III according to generator class and type (see 4.6.16). Cumulative brush or commutator wear shall
not exceed a total of 20 percent of the allowable wear during parts (a) and (b) of this test. Wear during part (c) shall
not exceed four percent of the allowable wear. Failure during this test shall be cause for rejection. Allowable
commutator wear shall be as specified by the manufacturer and approved by the procuring activity. During run 1 of
Table III, the blast cooling air flow shall be adjusted to the rated mass air flow as shown on Figure 6 or maximum
generator pressure drop, whichever occurs first. Airflow during subsequent runs shall be established by holding the
generator pressure drop constant at the value established in run 1. The generator shall be operated for at least 30
minutes and no more than 60 minutes additional operating time at continuous operating speed and rated load under
standard sea level conditions prior to each altitude run which is not preceded by a period of sea level operation in the
test schedule. The rate of change of altitude need not be controlled; however, temperature must remain within 10
degrees of the maximum temperature shown in Figures 1, 2 or 3, as applicable. The order in which the test runs are
performed is optional.
b. Type IV generators shall be operated for 100 hours at sea level maximum temperature cooling
conditions and for eight 12-hour cycles at the maximum altitude (see 4.6.14) and maximum temperature cooling
conditions for that altitude unless otherwise specified by the associated specification sheet.
Table II. Generator endurance test schedule. 1/
Generator
Class A
Class B
Class C
Type
Test
Cycles
Run 2/
Test
Cycles
Run 2/
Test
Cycles
Run 2/
Number
Part
Required
Number
Part
Required
Number
Part
Required
1
4
a
1
4
a
1
4
I
a
6
4
a
5
4
a
3
4
a
12
4
b
10
4
b
8
4
b
13
2
c
11
2
c
9
2
c
II
a
8
2
a
2
4
b
8
7
1
3
a
1
3
a
1
5
III
a
6
3
a
5
3
a
4
3
a
4
2
a
4
2
a
12
4
b
10
4
b
8
4
b
13
2
c
11
2
c
9
2
c
18
For Parts Inquires call Parts Hangar, Inc (727) 493-0744
© Copyright 2015 Integrated Publishing, Inc.
A Service Disabled Veteran Owned Small Business